
Throughout history, humanity has made attempts to create imagery through painting, sculptures and stories of anything that is meaningful to a person.
Houses, pets, families (or ourselves with the ‘selfie’) have been reproduced as a record of things as they were or as how we want to remember them. Technology has innovated this from cave paintings by our ancestors, to canvas, sculptures, photography and now 3D scanning.
Scanning over 30 years ago
In the 1980s a technique of 3D scanning was already in use, however it was inaccurate and relied upon metal probes to physically touch an object millions of times to collect location data points to create a model. The issue for archivists and collection specialists became that fragile and historical heritage items cannot be touched by scraping and sharp metal needles. Digital optical technology developed to make pathways for scanning to take place significantly faster and without physical contact. The limitations became computing power and storage space, and the last decade have seen those limitations fall away so far that the computing power of the moon landing is now held in our pockets.
3D scanning is in an emerging industry with community participation, corporate investment and general public usage. It could still be considered a niche interest but is gradually becoming a technology that is inserted into our everyday life.
Scanning today
Modern 3D Scanning is the use of one of two methods (structured white light or laser – discussed below) to create a digital record of an object in its three dimensional detail. It can be then presented for a variety of needs such as engineering or graphic presentation of the object. It allows people to observe objects and products in great detail and get as close to a hands on experience as possible without the object being present. Please explore the examples in our project to see the significant items we have scanned.
Stages
3D scans are developed over three steps. The object itself is scanned and then put into software to refine and add texture, as well as combine the point clouds if various scanner types have been moved.
Scanning and scanner types
The scanning technology is relatively established in concept but is refined more and more over time. As the users are generally a niche community, it is expected that the industry will have large jumps in quality of scanners and lower costs over the next decade. At this point there are two common forms discussed below.
Structured white light
A white light scanner projects a white light onto an object and measures the distortion to the shape of that projection through cameras angled differently to the projection. It uses intricate measurements of the angles that the light distortion at the points between the two cameras to identify a ‘point’ in reference to other locations.
The scanner will collect many points in very quick succession (one scan can number in the millions of points) and gather all these points to create a ‘point-cloud’ which goes into the post-scan software.
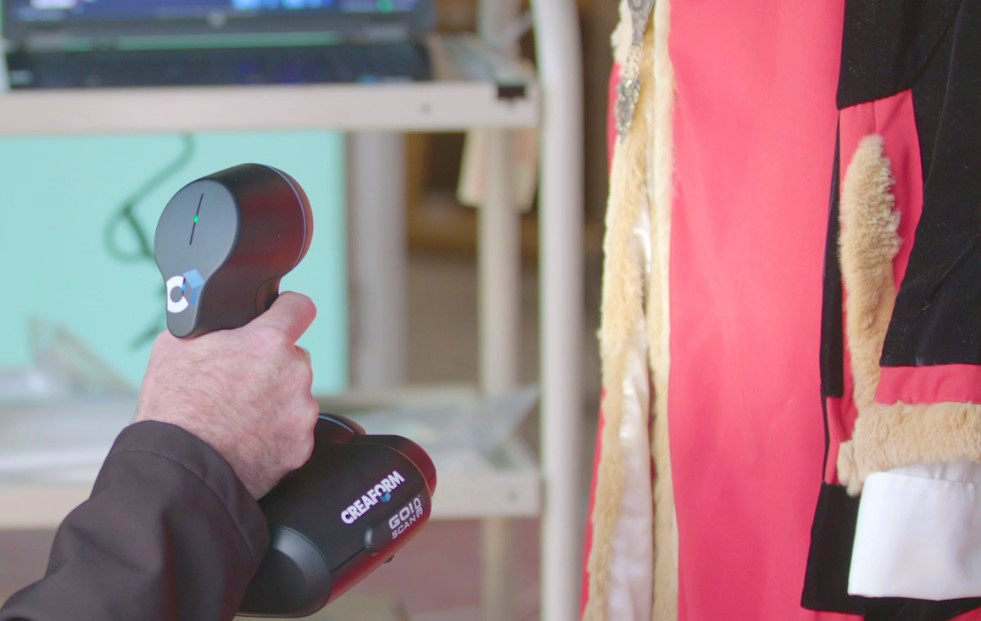
Laser
Laser scanners will create the same ‘point-cloud’ but will do it slightly differently. A laser scanner will work using where the laser line falls in an image taken by a camera. The laser is the brightest point of an image so the scanner will use this line to create the points. Sometimes in bright environments this will be tricky, but is overcome by the scanner turning the laser on and off quickly to find the line.
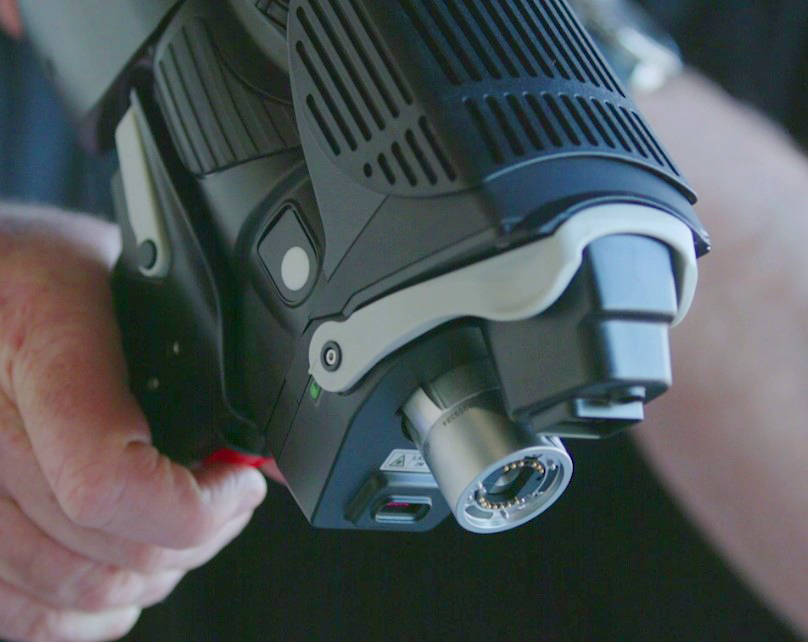
Point-Cloud Post-Processing
The point-cloud is not a 3D model until each of those points is connected in a ‘mesh’. The points are connected to each other in triangles, making each point into vertices’ of the model. Once this is done the texture is overlayed either with a captured layer or a plain texture.
This model can be exported into one of many file formats to finally be a completed 3D scan. For complex or larger items this process takes multiple days to it is very satisfying to get to this point.
When it is displayed the lighting, background and annotations need to be decided upon dependent upon context for the item or for where the scans will be displayed/used.
https://sketchfab.com/3d-models/mayoral-gown-wireframe-ba51fdcddcb44c4c8ad30bfdc9ad72ff
Wireframe 'Mesh' of the mayoral gown.
https://sketchfab.com/3d-models/mayoral-gown-matcap-8003afd32474437fb86d6ff056c7c8ef
3D model rendered from the above mesh
Challenges
3D scanners can capture almost anything you put in front of them regardless of size; however, there are some limitations including occluded areas (when parts of an object are hidden where the scanner can’t reach) very shiny and very dark objects are also difficult to scan and glass objects do not scan well.
We discovered that scans take a long time and are labour intensive and that the post-scanning work where the objects are refined in software is a difficult and lengthy process.
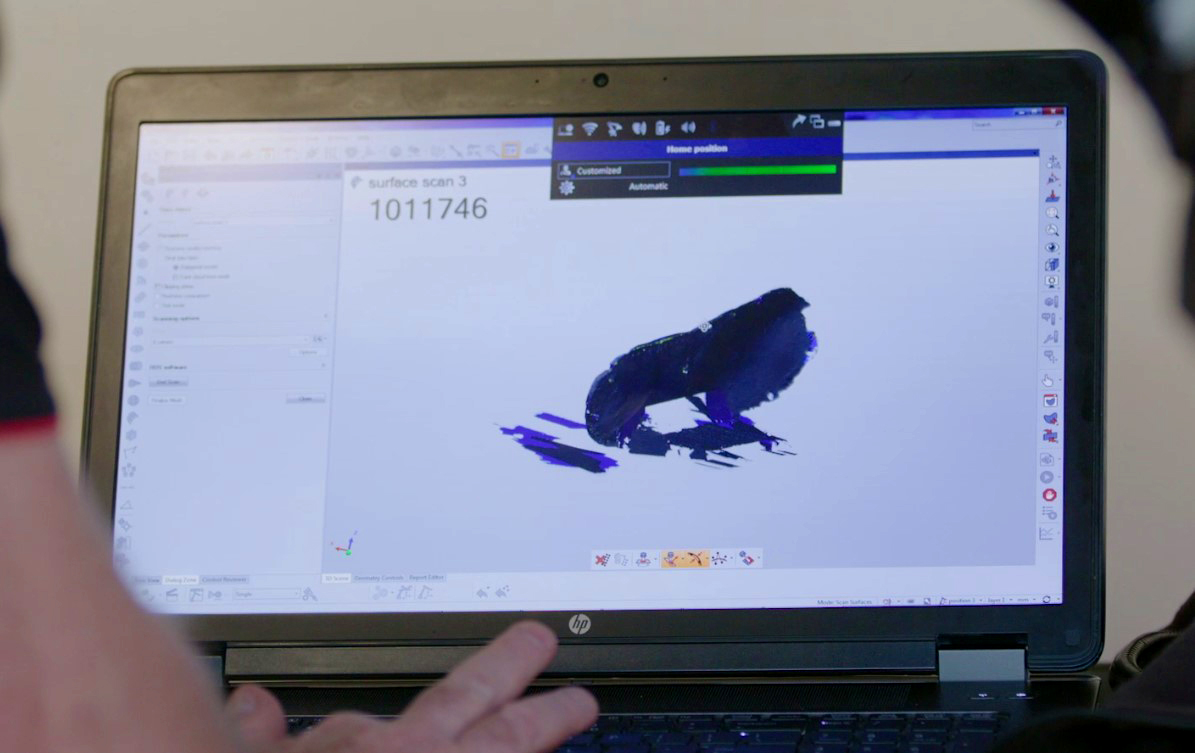
Can I DIY?
A wide range of 3D scanners are available in the market which all differ in price and quality. There are DIY 3D scanners that have to be put together like flat pack furniture and attachments that can be hooked onto your smartphone so you can scan on the go. Professional scanners are also available that can scan bigger items with higher levels of detail. As with most products there is a general price-quality relationship.
3D scanning can be done at home by enthusiasts and is a great hobby to do. There are free hosting sites like Sketchfab or p3d which are like Youtube for 3D scanning. Please keep in mind to do plenty of research before venturing into 3D scanning as it requires some technical know-how.
View all the objects City of Parramatta Council has scanned for the pilot project.
Joshua Jongma, Student Project Officer, Future City Unit, City of Parramatta, 2019
References
Brian Curless. 1999. From range scans to 3D models. SIGGRAPH Comput. Graph. 33, 4 (November 1999), 38-41.
Dixit, Ishan, Kennedy, Samantha, Piemontesi, Joshua, Kennedy, Bruce, & Krebs, Claudia. (2019). Which Tool Is Best: 3D Scanning or Photogrammetry - It Depends on the Task. Advances in Experimental Medicine and Biology, 1120, 107-119.
Fofi, David; T. Sliwa; Y. Voisin (January 2004). "A Comparative Survey on Invisible Structured Light". SPIE Electronic Imaging — Machine Vision Applications in Industrial Inspection XII. San Jose, USA. pp. 90–97.
Weise, T., Wismer, T., Leibe, B., & Van Gool, L. (2011). Online loop closure for real-time interactive 3D scanning. Computer Vision and Image Understanding, 635-648.